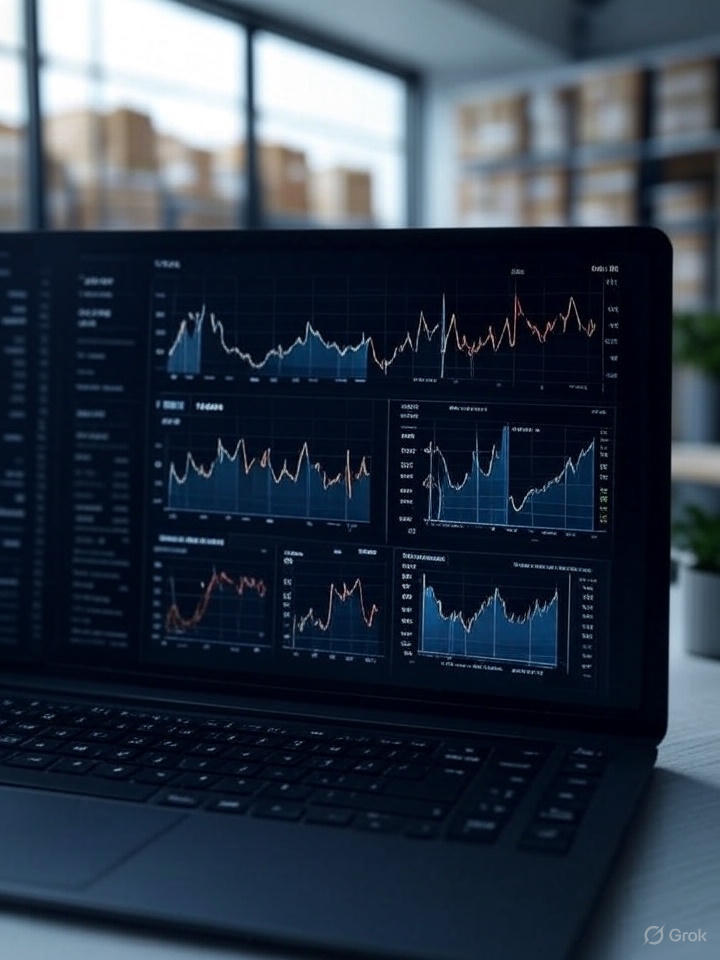
5 Ways Real-Time Inventory Tracking Reduces Operational Costs
Published on 4. July 2025 | Reading Time: 7 minutes
Every business owner knows that managing inventory feels like walking a tightrope. Hold too much stock, and you’re tying up valuable capital in products that aren’t moving. Hold too little, and you’re losing sales to competitors who can fulfill orders immediately. But what if there was a way to strike the perfect balance while significantly reducing your operational costs?
Enter real-time inventory tracking – a technology that’s transforming how businesses manage their stock and, more importantly, how much they spend doing it. Let’s explore five concrete ways that real-time inventory visibility can put money back in your pocket.
1. Eliminate Costly Stockouts and Overstock Situations
The Hidden Cost of Poor Inventory Balance
The Problem: Traditional inventory management often relies on periodic counts and educated guesses, leading to two expensive scenarios. You either run out of popular items (losing sales and customers) or you overstock slow-moving products (tying up cash and risking obsolescence).
The Real-Time Solution: With instant visibility into stock levels, you can maintain optimal inventory levels across all products. Real-time tracking shows you exactly when items are running low and provides historical data to predict future demand patterns.
Cost Savings Impact:
- Reduced lost sales from stockouts (studies show stockouts can cost retailers up to 4% of annual revenue)
- Lower carrying costs from excess inventory (typically 20-30% of inventory value annually)
- Decreased markdowns on slow-moving products
- Improved cash flow from optimized stock levels
Real-world example: A mid-sized electronics retailer reduced their inventory carrying costs by 25% within six months of implementing real-time tracking, freeing up $150,000 in working capital.
2. Slash Labor Costs Through Automated Processes
From Manual to Magical
The Problem: Manual inventory management is labor-intensive and error-prone. Employees spend countless hours counting stock, updating spreadsheets, and reconciling discrepancies. These tasks pull valuable resources away from customer service and revenue-generating activities.
The Real-Time Solution: Automated inventory tracking eliminates most manual processes. Stock levels update automatically as items are sold, received, or moved. Low-stock alerts trigger automatically, and reorder points can be set to generate purchase orders without human intervention.
Cost Savings Impact:
- Reduced labor hours spent on inventory management tasks
- Lower error rates that require time-consuming corrections
- Automated reordering eliminates manual purchase order creation
- Staff reallocation to higher-value activities like customer service
Conservative estimate: A typical retail business can reduce inventory-related labor costs by 30-40% through automation.
3. Minimize Shrinkage and Theft Losses
Real-Time Visibility = Real-Time Protection
The Problem: Inventory shrinkage due to theft, damage, or administrative errors can significantly impact your bottom line. Without real-time tracking, these losses often go unnoticed until the next physical count, making it difficult to identify when and where the loss occurred.
The Real-Time Solution: Instant inventory updates create an audit trail that makes discrepancies immediately visible. You can quickly identify unusual patterns or sudden stock level changes that might indicate theft or process issues.
Cost Savings Impact:
- Early detection of theft or shrinkage issues
- Reduced loss through improved accountability
- Better insurance claims with detailed tracking data
- Improved staff awareness when they know inventory is monitored in real-time
Industry data shows that businesses with real-time inventory tracking experience 40-60% less shrinkage compared to those using traditional methods.
4. Optimize Warehouse Operations and Reduce Fulfillment Costs
Efficiency Through Intelligence
The Problem: Inefficient warehouse operations drive up fulfillment costs through wasted time, incorrect shipments, and poor space utilization. Without real-time data, warehouse staff often struggle to locate items quickly or make optimal picking decisions.
The Real-Time Solution: Real-time inventory tracking provides instant location data and intelligent routing for warehouse operations. Staff can quickly locate items, optimize picking routes, and ensure accurate order fulfillment.
Cost Savings Impact:
- Faster order fulfillment through optimized picking routes
- Reduced shipping errors and associated return costs
- Better space utilization through real-time location tracking
- Improved customer satisfaction leading to repeat business
A warehouse study found that real-time inventory tracking reduced average order fulfillment time by 35% and shipping errors by 78%.
5. Eliminate Emergency Purchasing and Expedited Shipping Costs
Proactive Planning vs. Reactive Panic
The Problem: Running out of stock unexpectedly forces businesses into emergency purchasing mode. This means paying premium prices for rush orders, expedited shipping, and often accepting higher per-unit costs from secondary suppliers.
The Real-Time Solution: Real-time inventory tracking provides predictive insights that help you plan purchases well in advance. You can set up automated alerts for reorder points and use historical data to forecast demand patterns.
Cost Savings Impact:
- Elimination of rush order premiums (often 15-25% higher than standard pricing)
- Reduced expedited shipping costs (can be 3-10x normal shipping rates)
- Better supplier negotiations through planned, bulk purchasing
- Improved vendor relationships through consistent, predictable ordering
One manufacturing company reported saving $75,000 annually just by eliminating emergency purchases after implementing real-time inventory tracking.
The Compound Effect: How Small Savings Add Up
These five cost-reduction areas don’t work in isolation – they compound each other. When you reduce stockouts, you also reduce emergency purchases. When you automate processes, you also reduce errors and shrinkage. The total cost savings often exceed the sum of individual improvements.
Typical Cost Reduction Breakdown:
- Inventory optimization: 15-25% reduction in carrying costs
- Labor efficiency: 30-40% reduction in inventory-related labor
- Shrinkage reduction: 40-60% decrease in losses
- Operational efficiency: 20-35% improvement in fulfillment costs
- Purchasing optimization: 10-20% reduction in procurement costs
Getting Started: Implementation Considerations
Making the Business Case
Before implementing real-time inventory tracking, calculate your current costs in these five areas:
- Carrying costs from excess inventory
- Labor costs for manual inventory management
- Annual shrinkage losses
- Fulfillment inefficiencies and error costs
- Emergency purchasing premiums
Most businesses find that the cost savings from real-time inventory tracking pay for the system within 6-12 months.
Key Features to Look For
When evaluating real-time inventory tracking solutions, prioritize these cost-saving features:
- Automated reorder points and purchase order generation
- Multi-location visibility for businesses with multiple sites
- Integration capabilities with existing POS and accounting systems
- Mobile access for on-the-go inventory management
- Reporting and analytics for identifying cost-saving opportunities
The Bottom Line
Real-time inventory tracking isn’t just about knowing what you have – it’s about dramatically reducing what you spend to manage it. The five cost-reduction areas we’ve explored represent real, measurable savings that can transform your business’s profitability.
The question isn’t whether real-time inventory tracking will save you money – it’s how much you’re currently losing without it. Every day you delay implementation is another day of unnecessary operational costs eating into your profits.
Ready to start reducing your operational costs? The first step is understanding exactly how much your current inventory management approach is costing you. From there, the path to savings becomes crystal clear.
Want to calculate your potential cost savings from real-time inventory tracking? Contact our team for a free operational cost assessment and see how much you could save.